Status: Complete
Summary:
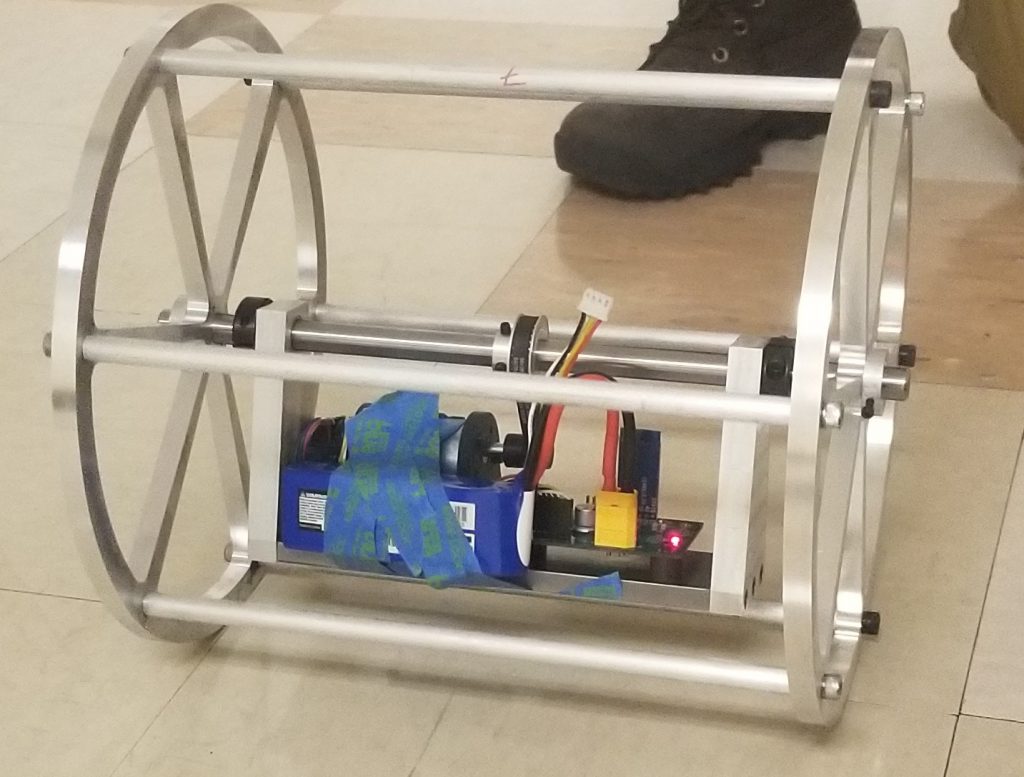
Analyzed system dynamics, set up PID control, produced
drawings for, and helped manufacture a robot under a
budget of $200 in three weeks with a team of four.
Skills: This project made use of CNC milling, Solidworks, Python, 3D printing, mechatronics, and control theory
Teammates: Michael Brown, Maheck Jerez, Nathan Barton
Timeline: May 2019, 3 weeks
Details
This project was completed with a team of four, including myself for the Introduction to Mechanical Design course, also known as ME14, at Caltech. For the second part of the course, students may elect to do an independent project, which passes a PDR and a CDR by the professor, the TAs, the shop manager, and the shop assistant. The very strict budget and intense timeline makes for a stressful but productive three weeks, with many long nights spent in the machine shop.
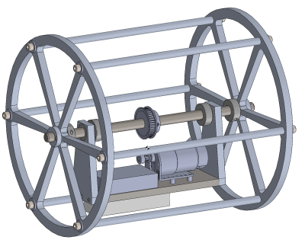
Our team wanted to do a project with quality machined parts and some controls element. The initial goals we set out to achieve for this project included:
- Maintain position on 15 degree slope
- Moving on level and angled surfaces
- PID control loop
- Machine a well-toleranced housing
- Successfully tune a responsive control loop
- Gain experience in assembling and tensioning belt drive assembly
Our fallback objectives and goals were:
- Produce movement on level surface
- Manual control
- Gain hands-on experience with controls (PID)
- Learn to implement RC communication
- Gain comfort working with assemblies
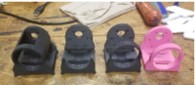
The simple pendulum-on-a-cart problem inspired this idea, a spool-shaped robot with an internal counterweight to help balance on a slope.
I worked out the system dynamics, simply a transformation of the initial condition variables we would be able to input to our code to tune the PID loop that would swing the counterweight. I also worked on the system dynamics and designed the mass of the counterweight to the mass of the robot, organizing the machining timeline and assembling and testing the robot.

This was one of the first projects I had done incorporating any sort of control system. Further improvements would incorporate data from the IMU to effectively reduce the wobble on start and stop